Ce site utilise des cookies afin que nous puissions vous fournir la meilleure expérience utilisateur possible. Les informations sur les cookies sont stockées dans votre navigateur et remplissent des fonctions telles que vous reconnaître lorsque vous revenez sur notre site Web et aider notre équipe à comprendre les sections du site que vous trouvez les plus intéressantes et utiles.
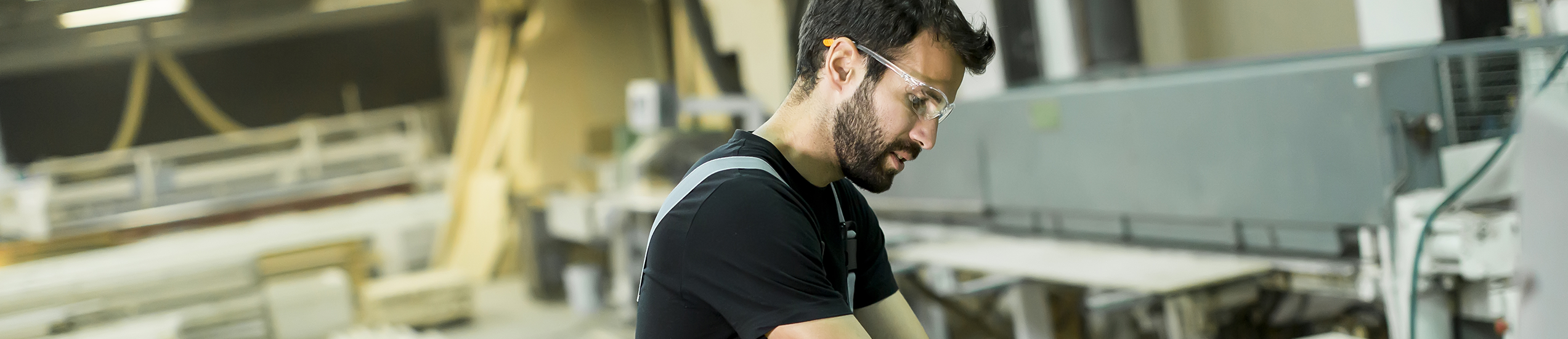
Client
Steinemann Technology AG est un leader mondial dans la production de machines de ponçage pour panneaux de bois et de systèmes de vernissage UV pour l’industrie graphique. Depuis plus de cent ans, l’entreprise fournit des solutions innovantes qui stimulent le développement du secteur manufacturier. Face à l’évolution des exigences opérationnelles et technologiques, Steinemann a dû moderniser son système de contrôle des machines, qui ne répondait plus aux standards UX actuels et limitait l’efficacité de la production. Le client recherchait une solution qui éliminerait non seulement les limitations actuelles, mais poserait également les bases pour une future numérisation et amélioration des processus de production.
Besoin du client
L’objectif du projet était la construction d’un nouveau système pour automatiser le processus de ponçage. La nouvelle solution devait améliorer l’efficacité de la production, augmenter la modularité, réduire les coûts de maintenance et assurer un meilleur contrôle qualité en conditions industrielles.
Steinemann s’est tourné vers nous pour élaborer une vision de l’évolution de son logiciel et pour mettre en œuvre de manière complète le nouveau système selon les meilleures pratiques. Le projet a été réalisé en étroite collaboration avec le client, ce qui a permis de clarifier en continu les exigences, de communiquer rapidement sur les risques et de co-créer des solutions optimales.
Chez Steinemann, la précision, l’efficacité et la reproductibilité sont à la base des activités. Cependant, l’ancien système de gestion de la qualité des panneaux est devenu un obstacle à un développement ultérieur.
Les plus grands problèmes comprenaient :
- Les données provenant des capteurs et des machines étaient traitées de manière synchrone avec de gros retards – les changements dans les paramètres du processus apparaissaient sur l’interface avec jusqu’à 10 secondes de retard. En pratique, cela empêchait les opérateurs de prendre des décisions en temps réel, car au moment où le problème apparaissait à l’écran, le produit pouvait déjà être mal usiné.
- Absence d’accès à distance et limitations dans la surveillance – le système de gestion de la qualité des panneaux ne fonctionnait que localement sur les machines, et le service informatique n’avait pas de possibilité de voir à distance le fonctionnement des équipements. L’absence d’accès centralisé compliquait le diagnostic des pannes, et l’absence de journaux d’événements empêchait l’analyse des problèmes.
- Interface utilisateur compliquée – les opérateurs devaient suivre de longues formations pour utiliser efficacement le système, et son utilisation nécessitait de nombreuses étapes manuelles.
- Difficultés dans la maintenance et le développement du système – l’introduction de modifications et de nouvelles fonctionnalités était chronophage et coûteuse. La modification d’un seul bouton pouvait prendre plusieurs mois. Le manque de modularité obligeait à intervenir dans toute l’application, et chaque mise à jour comportait un risque de nouveaux bugs.
Steinemann avait besoin d’une solution moderne qui augmenterait l’efficacité opérationnelle, améliorerait le confort de travail des opérateurs et permettrait une extension facile du système à l’avenir.
Solution
Pour répondre aux attentes du client, nous avons proposé de créer un nouveau système de gestion de la qualité des panneaux à partir de zéro – conçu pour une architecture moderne, une haute disponibilité des données et une utilisation intuitive. Les décisions les plus importantes du projet comprenaient le choix d’une architecture modulaire basée sur des conteneurs (Docker) et l’intégration à l’infrastructure industrielle existante du client. Le nouveau système BQC Automation a été conçu comme une solution conteneurisée stable et fiable, facile à déployer et à mettre à jour sur plusieurs machines simultanément. Grâce à la conteneurisation, les futures mises à jour logicielles peuvent être effectuées sans interruption, ce qui réduit considérablement le temps de livraison des correctifs et des nouvelles fonctionnalités par rapport à l’ancien système.
Architecture du système basée sur OPC Connector
OPC Connector est un module intermédiaire qui communique avec les machines et les capteurs de l’usine. OPC collecte en temps réel les données de processus (par exemple, vitesse des rouleaux, consommation électrique, épaisseur des panneaux poncés), les traite et envoie, si nécessaire, des commandes de retour aux dispositifs de contrôle. Cela permet de fermer la boucle de régulation – le système peut ajuster automatiquement les paramètres de la machine afin de maintenir une qualité de production stable.
Nous avons développé un algorithme spécial de contrôle qualité du ponçage, qui régule en temps réel la charge de la machine sur la base des données des capteurs, évitant ainsi sa surcharge et garantissant une qualité répétable de chaque panneau.
Grâce à la nouvelle architecture, toutes les données de production sont immédiatement disponibles – nous avons réduit le délai de lecture des paramètres à <100 ms, ce qui signifie en pratique que le travail s’effectue en temps réel. L’ancien système actualisait les données environ toutes les 10 secondes. Une telle amélioration de la réactivité a été rendue possible notamment grâce à l’extraction d’un connecteur OPC dédié – une couche de communication séparée avec la machine, ce qui a accéléré la transmission des données (auparavant, la gestion OPC était « intégrée » dans le code de l’ancienne application et fonctionnait de manière inefficace).
Nouvelle interface utilisateur
Nous avons accordé une grande importance à la nouvelle interface utilisateur. Notre objectif était de créer un système de gestion de la qualité du ponçage aussi convivial que possible pour les opérateurs de machines, afin d’augmenter la productivité et de réduire la fréquence des erreurs humaines.
Dans ce domaine, nous avons mené une analyse UX de la solution existante avec le client et, sur cette base, nous avons pris plusieurs décisions de conception importantes :
- Simplification de l’interface — la nouvelle application ne contient que les fonctions nécessaires, et la disposition des écrans a été repensée pour réduire la charge cognitive de l’utilisateur et faciliter la navigation. Les étapes et informations inutiles, qui distrayaient les opérateurs dans l’ancien système, ont été éliminées.
- Intuitivité — nous avons utilisé des modèles de conception UX/UI modernes, grâce auxquels le système est plus intuitif et en adéquation avec les attentes des utilisateurs habitués aux applications actuelles. Les éléments de commande sont regroupés de manière logique, et les alertes et messages sont formulés de manière compréhensible. Tout cela réduit le temps nécessaire à la formation des nouveaux opérateurs.
- Personnalisation et flexibilité — le nouveau logiciel a été conçu de manière modulaire, ce qui permet d’adapter les fonctions aux besoins spécifiques de chaque usine. Si nécessaire, des modules complémentaires peuvent être ajoutés au système de base sans modifier le cœur de l’application.
Les administrateurs ont désormais la possibilité de configurer les autorisations et l’interface pour différents rôles utilisateurs (par ex. opérateur, ingénieur, manager) – chacun voit donc uniquement les fonctions dont il a besoin.
Le système propose également une interface web accessible via un navigateur (Chrome, Firefox, Edge). Il peut être lancé sur n’importe quel ordinateur ou tablette du réseau de l’usine, sans qu’il soit nécessaire d’installer un logiciel dédié sur chaque machine. L’interface est responsive et adaptée aux conditions industrielles difficiles (par ex. lisibilité sur les grands écrans dans l’usine).
La nouvelle solution a été adaptée pour fonctionner dans un écosystème plus large
Le système communique non seulement avec les machines via OPC, mais aussi avec des plateformes externes, telles que le cloud Azure du client. Les données de production peuvent être envoyées vers le cloud, ce qui ouvre la voie à une supervision à distance, une infrastructure évolutive et une analyse de données pour une optimisation ultérieure. Nous avons également pris soin d’intégrer des mécanismes de sécurité et de fiabilité. Le système dispose d’un tampon de données local en cas de perte de connexion au réseau. Ainsi, même en cas de panne de liaisons internet, le fonctionnement de la machine et la collecte des données de qualité ne sont pas interrompus.
Méthodologie 4D éprouvée
Compte tenu de la complexité du projet et des objectifs commerciaux du client, nous avons décidé d’utiliser notre méthodologie 4D (Discovery, Definition, Delivery, Direction), soutenue par une approche Agile et des techniques de Design Thinking. Ce modèle de travail a permis une livraison itérative des résultats avec un contrôle qualité et des risques constant.
- Lors de la phase Discovery, nous nous sommes concentrés sur une compréhension complète des besoins des utilisateurs et des problèmes à résoudre – notamment via des ateliers avec les ingénieurs de Steinemann, l’analyse du processus de ponçage et l’examen du système de gestion de la qualité existant.
- Ensuite, dans la phase Definition, nous avons précisé les exigences (fonctionnelles et non fonctionnelles), préparé des concepts UX et conçu l’architecture cible du système. Grâce au prototypage rapide, nous avons pu valider tôt avec le client les hypothèses clés et apporter les corrections nécessaires avant l’implémentation proprement dite.
- Lors de la phase Delivery, l’un des plus grands défis techniques fut l’intégration avec la machine via OPC. Le développement d’un connecteur fiable a nécessité une coopération étroite entre nos développeurs et les ingénieurs du client, mais nous avons finalement réussi à établir une connexion stable et rapide. En parallèle, nous avons peaufiné l’algorithme de contrôle qualité automatique du ponçage, qui a dû être validé dans des conditions de production réelles. À cette fin, notre équipe a visité deux fois l’usine du client et effectué des tests directement sur les lignes de production. Ces tests « en direct » ont assuré que la solution développée fonctionne comme prévu et améliore effectivement la qualité des produits. Les deux dernières semaines du projet ont été consacrées exclusivement aux tests – automatiques et manuels, y compris des tests d’acceptation avec les futurs utilisateurs. Cela nous a permis de détecter et de corriger les derniers défauts avant la mise en production.
- Direction – c’est-à-dire le déploiement et le support post-lancement. Après avoir terminé les travaux de développement, nous avons formé les opérateurs et assisté au démarrage du système sur la première ligne de production. Le nouveau système de gestion de la qualité du ponçage a été mis en œuvre en parallèle avec l’ancien système (en mode pilote) afin de comparer en toute sécurité leur fonctionnement. Les opérateurs ont très bien accueilli la nouvelle interface, la trouvant claire et facile à utiliser, ce qui a confirmé nos hypothèses sur la réduction du temps d’apprentissage. Durant les premières semaines suivant le lancement, notre équipe a assuré un support constant comme le suivi à distance ou une réponse rapide aux questions des utilisateurs. Après la phase de démarrage pilote, le client a décidé d’étendre progressivement le nouveau système à d’autres machines et lignes de production. Enfin, nous avons transmis à Steinemann toute la documentation d’exécution ainsi que des recommandations pour le développement futur du système.
Résultats
La mise en œuvre du nouveau système a facilité le travail quotidien des opérateurs, ainsi que la gestion globale du processus de production.
Le client a constaté une amélioration significative de l’efficacité et de la qualité du processus de ponçage des panneaux. Grâce à l’automatisation du contrôle qualité, la machine ajuste ses paramètres en temps réel, ce qui a permis d’obtenir des produits plus homogènes en termes de qualité et de réduire le nombre de rejets.
Les opérateurs ont désormais une vue en temps réel du processus. Les données et indicateurs clés sont immédiatement disponibles sur des tableaux de bord lisibles. Nous avons éliminé le problème des retards de données. Les décisions opérationnelles peuvent être prises instantanément, et le système génère des alertes automatiques dès qu’une anomalie est détectée.
La nouvelle interface utilisateur est conviviale et intuitive. Le temps de formation des nouveaux employés est passé de plusieurs jours à seulement quelques heures.
Grâce à sa construction modulaire et à sa configuration flexible des rôles, le système favorise la collaboration entre les différents départements. Les opérateurs se concentrent sur leurs tâches, tandis que les ingénieurs procédés ou les responsables de production accèdent à des analyses avancées sans interférer dans le travail des opérateurs.
L’unification de l’environnement du système de gestion de la qualité du ponçage a permis de remplacer de nombreux postes dispersés par un système centralisé. Au lieu d’entretenir plusieurs écrans et ordinateurs pour chaque machine, un simple terminal avec navigateur suffit désormais. Cela se traduit par des coûts moindres en matériel et en maintenance. La modernisation du logiciel a également prolongé le cycle de vie des machines – grâce au suivi continu de leur état et aux ajustements automatiques de la charge, les machines sont moins sujettes aux pannes dues à de mauvais réglages.
L’ensemble de l’investissement a créé une base solide pour de futures améliorations. L’entreprise Steinemann dispose désormais d’une plateforme moderne, pouvant être étendue à des fonctionnalités telles que l’analyse avancée des données de production, des mécanismes de maintenance prédictive ou une intégration avec d’autres systèmes de l’usine.
Technologies
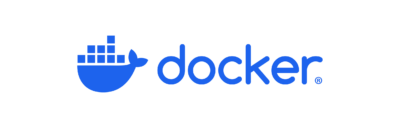

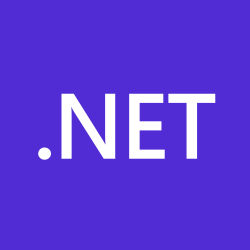
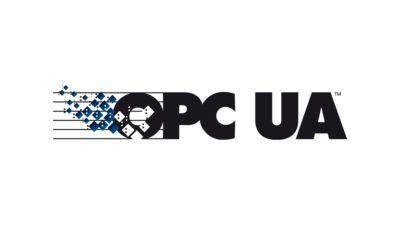
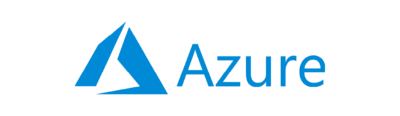
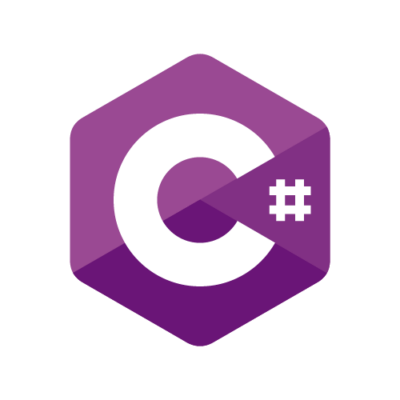
Client
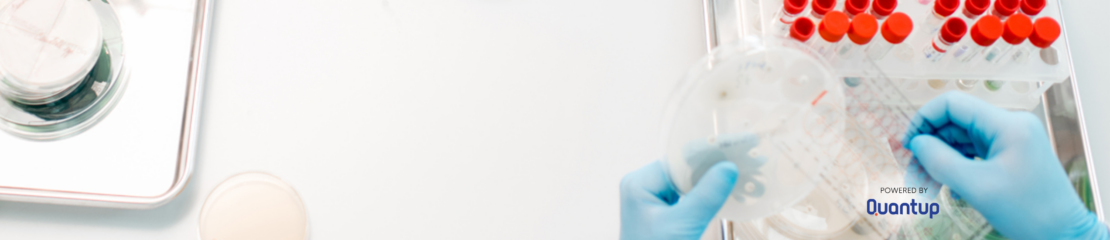
Utilisation de l’IA/ML pour l’identification des souches bactériennes à partir des motifs de Fresnel
Conception, développement, DevOps ou Cloud - de quelle équipe avez-vous besoin pour accélérer le travail sur vos projets ?
Discutez avec vos partenaires de consultation pour voir si nous sommes compatibles.
Jakub Orczyk
Membre du Conseil d’administration/Directeur des ventes VM.PL
Réservez une consultation gratuite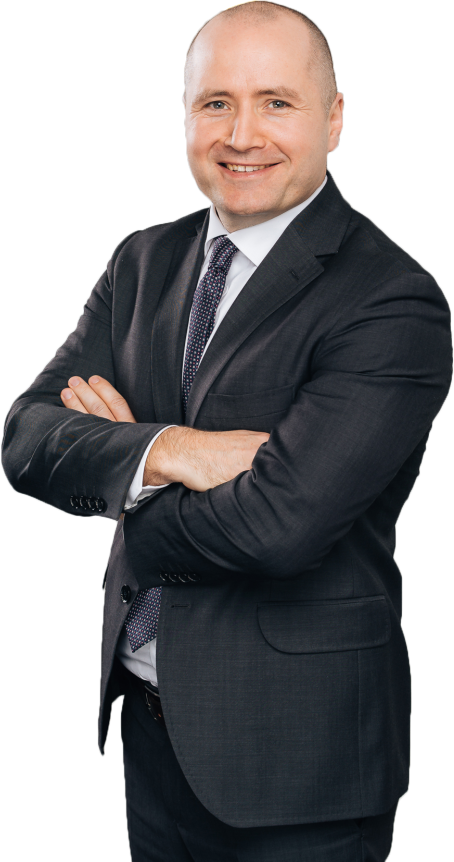